In today’s competitive electronics market, reducing PCB costs is crucial for manufacturers and designers alike. By optimizing design processes and sourcing materials wisely, companies can significantly lower expenses without sacrificing quality. This article explores effective strategies for cutting PCB costs, ensuring businesses can stay ahead while maintaining high standards.
Understanding PCB Costs
Understanding PCB costs involves recognizing key elements that influence pricing. By identifying these factors, manufacturers can make informed decisions to manage expenses effectively.
Factors Affecting PCB Pricing
- Material Selection: Choosing materials like FR-4, polyimide, or aluminum affects costs significantly. Higher quality materials often lead to increased prices.
- Layer Count: The number of layers in a PCB influences complexity and cost. Simple designs with fewer layers are generally cheaper to produce.
- Board Thickness: Thicker boards may incur higher costs due to additional material usage and manufacturing processes.
- Surface Finish: Different finishes, such as ENIG or HASL, have unique costs. The choice impacts solderability and reliability.
- Quantity Ordered: Larger production volumes typically reduce per-unit costs. Bulk purchasing often leads to discounts.
- Manufacturing Processes: Techniques like automated assembly or manual soldering affect labor costs and overall pricing.
- Design Complexity: More intricate designs require additional manufacturing time and increase costs.
The Importance of Cost Management
Cost management in PCB production holds substantial importance. Effective management ensures competitiveness in the market while maintaining quality.
- Profit Margins: Keeping costs low maintains healthy profit margins, allowing for pricing flexibility.
- Budget Control: Monitoring expenses helps prevent overspending on materials and production, promoting financial stability.
- Resource Allocation: Efficient cost management directs resources to critical production areas, enhancing productivity.
- Supplier Negotiations: Understanding costs enables better negotiations with suppliers, securing favorable terms for materials.
- Market Responsiveness: Effective cost management allows for quick adaptations to market demands, ensuring relevancy and customer satisfaction.
Design Considerations for Cost Reduction
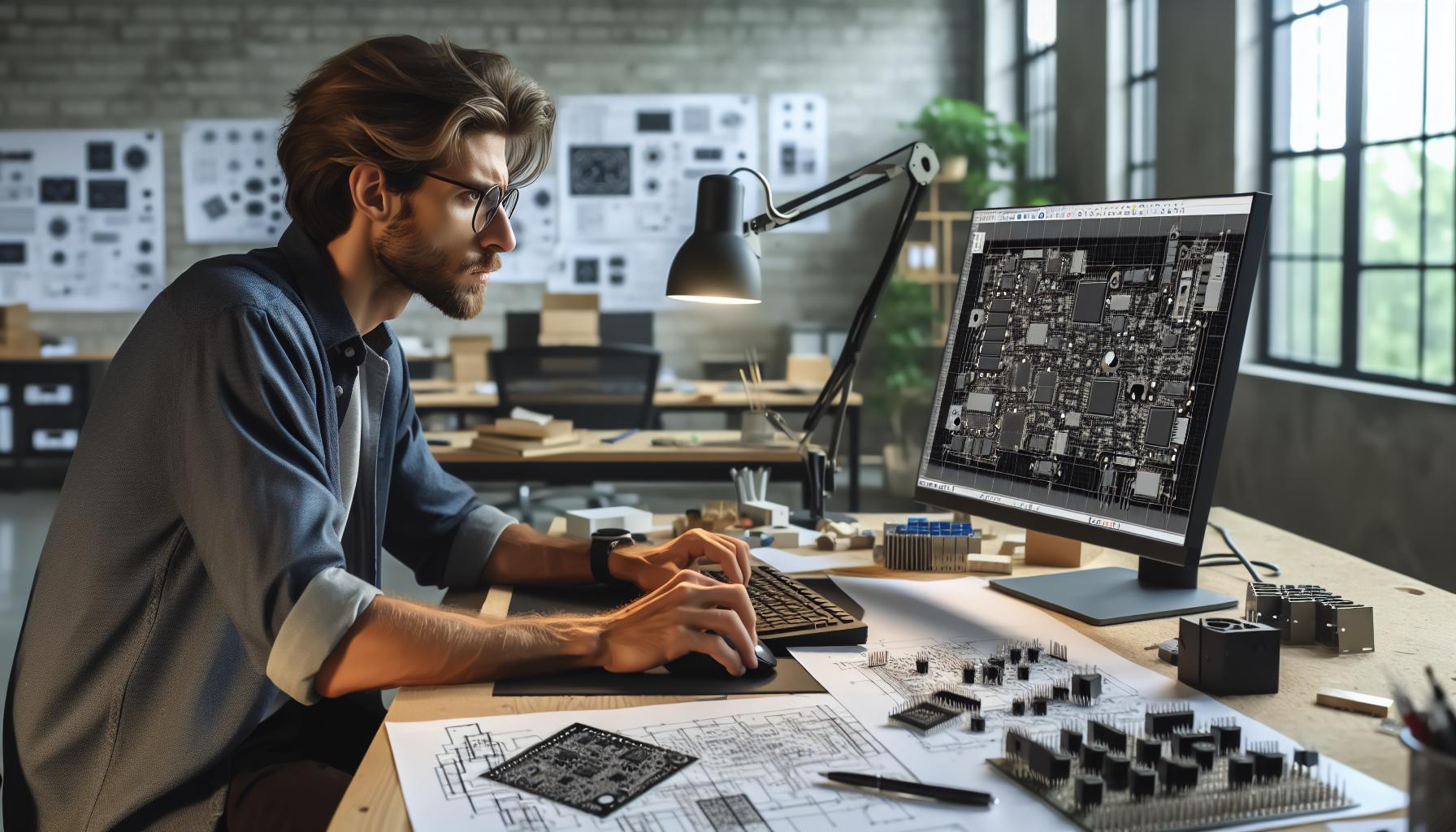
Reducing PCB costs starts with thoughtful design decisions. Key factors such as layout simplicity and material choice impact pricing directly.
Simplifying PCB Layout
Streamlined layouts minimize material use and manufacturing complexity. Designers should aim for fewer layers, shorter traces, and less intricate routing. Reducing unnecessary components and optimizing the placement of essential ones decreases the overall area of the board. Using automated design tools for layout checks can highlight opportunities for simplification while preserving functionality.
Choosing the Right Materials
Material selection significantly affects PCB costs. Opt for standard materials rather than specialized ones when possible. FR-4 remains the most commonly used substrate due to its balance of performance and affordability. Additionally, consider thickness; thinner boards can save material costs but ensure they meet strength requirements. Evaluate copper weight, as choosing lower copper thickness can reduce expenses without sacrificing performance. Balancing cost and quality ensures the PCB meets required specifications while remaining within budget constraints.
Manufacturing Techniques to Lower Costs
Manufacturers can implement specific techniques to reduce PCB production costs without compromising quality.
Batch Production vs. Single Units
Batch production reduces overall costs compared to manufacturing single units. Producing multiple PCBs simultaneously allows for economies of scale, where the average cost per unit decreases with higher quantities. This method minimizes setup times and optimizes machine efficiency. Firms achieving higher production runs often negotiate better material prices and reduce labor costs, leading to substantial savings. In contrast, single-unit production typically incurs higher costs due to increased setup and labor expenses.
Optimizing Production Processes
Optimizing production processes enhances cost efficiency in PCB manufacturing. Streamlining workflows and using automated machinery can significantly decrease labor costs and minimize errors. Implementing lean manufacturing principles also improves resource allocation and reduces waste. Regular maintenance of equipment ensures consistent quality and reduces downtime. Additionally, utilizing advanced technologies, such as computer-aided design (CAD) and manufacturing (CAM) software, assists in optimizing designs for manufacturability, thereby further lowering expenses in the long run.
Sourcing Components Efficiently
Sourcing components efficiently plays a vital role in reducing PCB costs. Understanding supplier options and negotiating bulk purchases can lead to significant savings.
Evaluating Supplier Options
Evaluating supplier options requires a systematic approach. He or she must assess the reliability, quality, and pricing of potential suppliers. Key factors include:
- Supplier Reputation: Research online reviews and testimonials from previous customers. Reliable suppliers tend to have positive feedback and strong industry presence.
- Lead Times: Consider the lead times for component delivery. Shorter lead times can reduce production delays, impacting overall costs.
- Quality Assurance: Check for certifications like ISO 9001. Certified suppliers adhere to quality standards that minimize defects, lowering costs in the long run.
- Technical Support: Look for suppliers offering technical support. Access to expertise can prevent issues that lead to costly delays.
Negotiating Bulk Purchases
Negotiating bulk purchases maximizes cost savings on components. Strategic negotiation can secure better pricing structures. Effective strategies include:
- Volume Discounts: Request volume discounts based on projected orders. Suppliers often lower prices significantly for larger orders.
- Payment Terms: Negotiate favorable payment terms. Extended payment periods can improve cash flow, aligning expenses with revenue generation.
- Long-Term Partnerships: Consider establishing long-term relationships with suppliers. Loyal customers often receive preferential pricing and service.
- Comparison Quotes: Gather multiple quotes from different suppliers. Comparing offers enables better negotiation use, resulting in optimal pricing.
Efficient sourcing contributes directly to PCB cost reductions, enhancing overall production efficiency.
Utilizing Technology for Cost Efficiency
Technology plays a vital role in enhancing cost efficiency in PCB production. By adopting advanced software and automation, manufacturers can significantly reduce expenses while maintaining quality.
Software Tools for Design and Simulation
Software tools streamline the design and simulation process, leading to cost reductions. Programs like Altium Designer, Eagle, and KiCAD allow designers to create precise layouts and run simulations, identifying potential issues early. Early detection minimizes costly changes during manufacturing. Additionally, these tools optimize resource utilization, reducing material waste. They enable rapid prototyping, allowing for quick iterations and faster time-to-market. Overall, these software solutions improve design accuracy and efficiency.
Automation in PCB Manufacturing
Automation transforms PCB manufacturing by improving productivity and minimizing labor costs. Automated systems perform repetitive tasks such as soldering, assembly, and inspection quickly and accurately. This technology reduces errors and increases throughput, translating to lower production costs. The integration of robotic assembly lines and automated testing systems ensures consistency in quality while reducing setup times. Investing in automation technologies can yield significant long-term savings due to decreased labor reliance and increased production capacity.
Conclusion
Reducing PCB costs is essential for staying competitive in the electronics industry. By focusing on design optimization, material selection, and efficient manufacturing processes, manufacturers can achieve significant savings without sacrificing quality.
Embracing advanced technologies and automation further enhances cost efficiency while minimizing errors. Strategic component sourcing and strong supplier relationships also play a crucial role in achieving lower costs.
For a precise cost estimate, requesting a pcb quotation from multiple suppliers can help businesses compare prices and make informed financial decisions.
With a proactive approach to cost management and a commitment to quality, manufacturers can navigate the challenges of the market effectively and thrive in an ever-changing landscape.
Frequently Asked Questions
What are PCBs and why are they important?
Printed Circuit Boards (PCBs) are essential components in electronic devices that provide the electrical connections needed for operation. They are vital for circuit assembly, affecting device performance and reliability.
How can manufacturers reduce PCB costs?
Manufacturers can reduce PCB costs by optimizing design processes, simplifying layouts, using standard materials, and choosing efficient manufacturing techniques. Bulk sourcing components and negotiating better terms with suppliers also play a crucial role.
What factors influence PCB pricing?
Key factors that influence PCB pricing include material selection, layer count, board thickness, surface finish, order quantity, manufacturing processes, and overall design complexity.
Why is cost management important in PCB production?
Cost management is crucial in PCB production as it helps maintain profit margins, control budgets, allocate resources efficiently, and respond to market demands while ensuring high quality standards.
What design strategies can reduce PCB costs?
Design strategies to reduce PCB costs include minimizing layer count, optimizing component placement, shortening trace lengths, and simplifying layouts to reduce material use and manufacturing complexity.
How do manufacturing techniques affect PCB costs?
Manufacturing techniques impact PCB costs significantly; batch production is generally more cost-effective than single-unit production. Streamlined workflows and automation further enhance efficiency and reduce expenses.
What is the role of efficient component sourcing in reducing PCB costs?
Efficient component sourcing involves evaluating suppliers, negotiating bulk purchases, and establishing long-term partnerships, which can result in volume discounts and improved production efficiency, ultimately leading to cost reductions.
How does technology contribute to PCB cost efficiency?
Technology, such as advanced software tools and automation, streamlines the design and production process. Early issue detection and automated systems minimize labor costs and errors, improving overall cost efficiency in PCB manufacturing.