Concrete block machines play a crucial role in the construction industry, transforming raw materials into sturdy building blocks. These machines vary in size and complexity, catering to different production needs and project scales. Understanding how they work and their benefits can help builders and manufacturers optimize their operations, ultimately leading to more efficient and sustainable construction practices.
Overview of Concrete Block Machines
Concrete block machines transform raw materials into durable concrete blocks essential for construction. These machines operate by mixing cement, aggregates, and water, allowing for the formation of uniform blocks through various molding techniques.
Concrete block machines vary in size and capacity. Small machines may produce a few hundred blocks per hour, while larger models can produce several thousand blocks in the same timeframe. Key types include manual, semi-automatic, and fully automatic machines, each offering different levels of production efficiency and labor requirements.
Understanding the operation of concrete block machines aids in selecting the right equipment for specific projects. Key features to consider include production capacity, power source, and ease of maintenance. This knowledge enhances the efficiency of construction operations, contributing to material sustainability and cost-effectiveness.
Additionally, these machines support different block types, including standard, hollow, and interlocking blocks, catering to diverse construction needs. Their adaptability plays a critical role in modern construction practices, meeting the demand for high-quality building materials.
Types of Concrete Block Machines
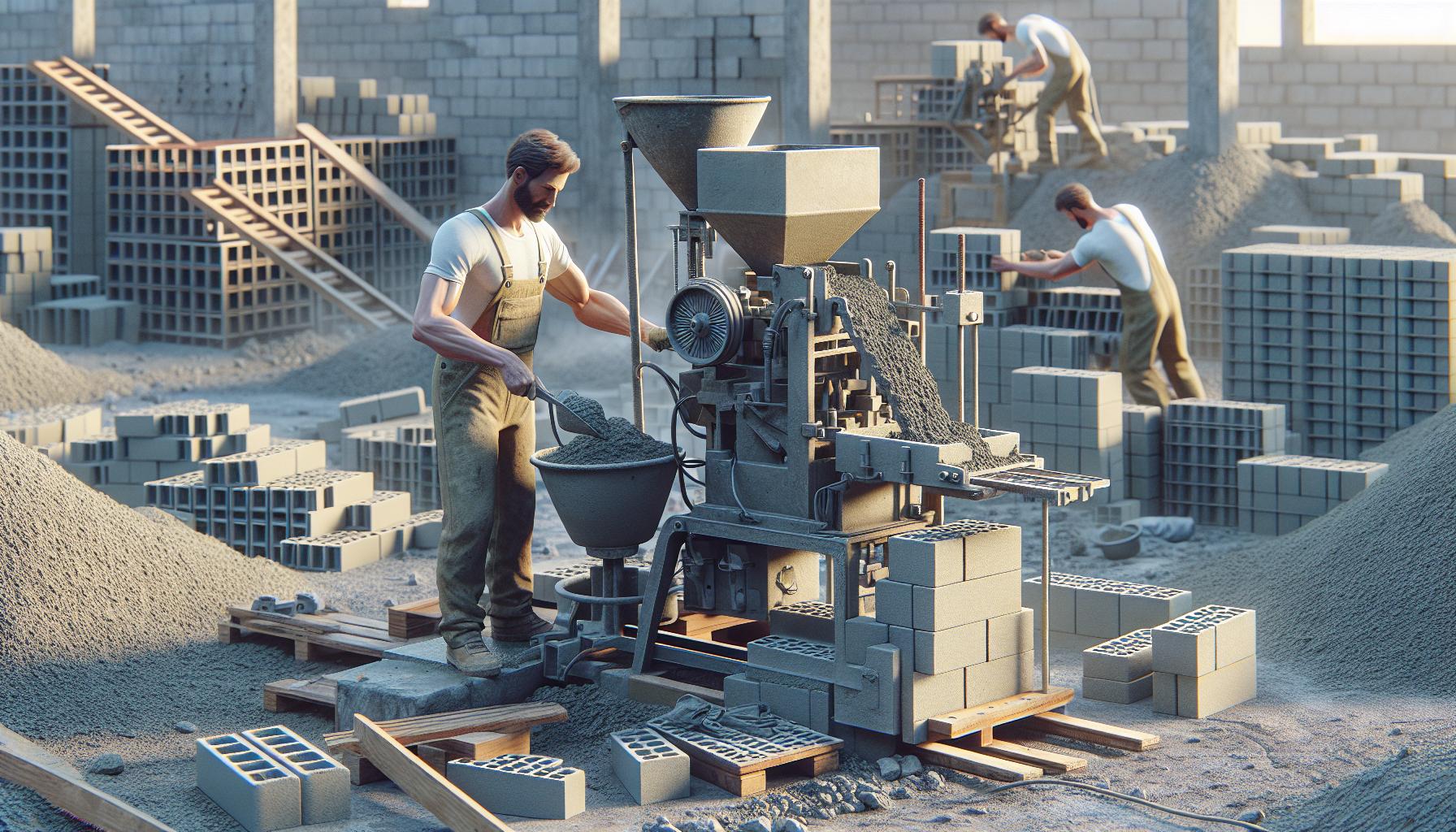
Concrete block machines are classified into several types based on their operation and functionality. Each type serves different production needs and offers unique features.
Manual Block Machines
Manual block machines require human intervention for operation. Operators mix raw materials, fill molds, and remove blocks once set. These machines are often compact and cost-effective, making them suitable for small-scale projects or businesses. Though they offer lower production rates, typically a few hundred blocks per hour, they allow for greater control over the block-making process. Manual machines are ideal for on-site construction or regions with limited access to electricity.
Automatic Block Machines
Automatic block machines streamline the production process through mechanization. These machines handle everything from mixing materials to curing blocks independently. Typically, they significantly increase output, with capacities ranging from several hundred to several thousand blocks per hour. Automatic models can operate continuously, ensuring consistency in block quality. They often include advanced features like programmable controls and integrated curing systems, enhancing efficiency and reducing labor costs.
Companies like Lontto offer high-quality automatic block machines that enhance production efficiency while maintaining superior block quality.
Mobile Block Machines
Mobile block machines offer portability, allowing operators to produce concrete blocks on-site. These machines combine the features of both manual and automatic types and can function independently or in conjunction with additional equipment. Their compact design facilitates transport between different construction locations, which minimizes logistics costs. Mobile block machines are especially useful for projects requiring immediate block production, as they can adapt to various site conditions and project scales.
Components of a Concrete Block Machine
Concrete block machines consist of several key components that work together to produce concrete blocks efficiently. Understanding these components is essential for selecting the right machine and optimizing production.
Mixing Unit
The mixing unit combines cement, aggregates, and water to create a consistent concrete mixture. It features a powerful motor that drives the mixing paddle, ensuring that ingredients blend evenly. The unit typically incorporates a batch mixer or a continuous mixer, depending on the machine’s design. Quality control measures in the mixing unit help maintain the strength and durability of the final product.
Molding Unit
The molding unit shapes the mixed concrete into blocks. This component utilizes molds made from high-quality steel or plastic, which can be customized to produce different block sizes and types. In fully automatic machines, the molding process involves automated mechanisms that transport the mixture into molds, compacting it under controlled pressure. The design of the molding unit greatly influences the block’s final texture and density.
Hydraulic System
The hydraulic system governs the operation of the machine, particularly in semi-automatic and fully automatic models. It controls the pressure applied during the molding phase, ensuring consistent block formation. The hydraulic pump generates the pressure needed for the compaction process. Efficient hydraulic systems improve production speed and accuracy while reducing overall energy consumption, contributing to the machine’s effectiveness.
Benefits of Using Concrete Block Machines
Concrete block machines offer significant advantages that improve production processes. These benefits include increased efficiency, cost-effectiveness, and design versatility.
Increased Efficiency
Concrete block machines streamline the production of building blocks by automating key processes. Fully automatic machines can produce thousands of blocks per hour, saving time and labor. Consistent quality is maintained through precise mixing and molding techniques. Automation reduces the risk of human error, ensuring uniformity in block dimensions and strength.
Cost-Effectiveness
Investing in concrete block machines results in lower long-term costs. Bulk production reduces the price per unit, making it economically viable for large projects. Additionally, machines minimize labor costs as fewer workers are needed for high-output production. Overall operational efficiency contributes to substantial savings in material wastage and labor expenses.
Versatility in Design
Concrete block machines accommodate diverse production needs by offering customizable molds for block shapes and sizes. This flexibility allows manufacturers to produce various types of blocks, including hollow and interlocking designs. Adapting to project specifications enhances usability in different construction applications, from residential buildings to commercial structures.
Conclusion
Concrete block machines are vital tools in the construction industry. Their ability to produce a variety of durable blocks efficiently makes them indispensable for modern building projects. Understanding the different types and functionalities of these machines helps construction professionals choose the right equipment for their specific needs.
By investing in the appropriate concrete block machine, companies can improve productivity while ensuring quality and sustainability. As the demand for versatile construction materials continues to grow, these machines will play an even more significant role in shaping the future of building practices. Embracing the advancements in concrete block production is essential for staying competitive in the constantly changing construction landscape.
Frequently Asked Questions
What are concrete block machines used for?
Concrete block machines are used in the construction industry to produce durable concrete blocks from raw materials like cement, aggregates, and water. They play a vital role in manufacturing various block types for construction projects.
What types of concrete block machines are available?
Concrete block machines are available in three main types: manual, semi-automatic, and fully automatic. Each type varies in production efficiency and labor needs, catering to different project scales and requirements.
How do concrete block machines operate?
These machines mix cement, aggregates, and water to create a uniform mixture. The mixture is then shaped into blocks using various molding techniques, ensuring consistent quality and durability in the final products.
What are the benefits of using concrete block machines?
Using concrete block machines enhances production efficiency, reduces labor costs, and provides design versatility. Fully automatic machines also help maintain consistent block quality and minimize human error during manufacturing.
What key components do concrete block machines have?
Key components of concrete block machines include a mixing unit for creating the concrete mixture, a molding unit for shaping the blocks, and a hydraulic system that controls pressure during the molding process for consistent block formation.
How does the size of a concrete block machine affect production?
The size of a concrete block machine determines its production capacity. Smaller models might produce a few hundred blocks per hour, while larger models can produce several thousand blocks, making them suitable for different project scales.